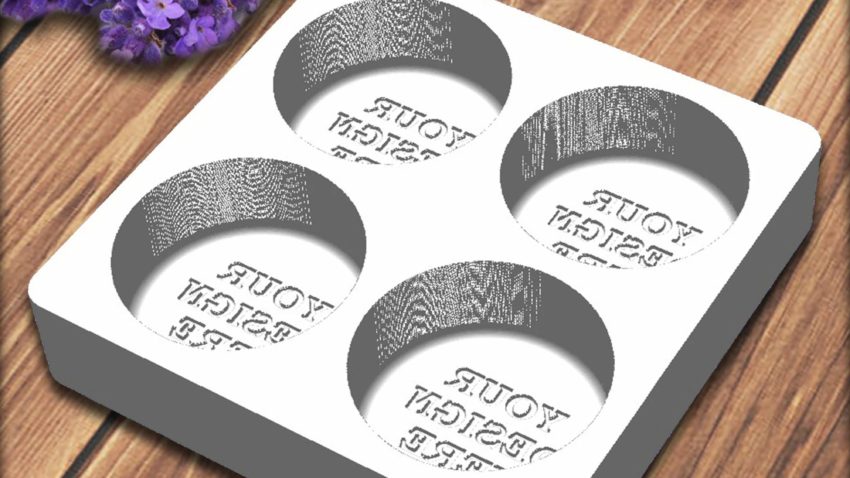
How To Make Professional Soap Making Molds With Rubber
How to make professional soap-making molds with rubber starts with a well-crafted model. The model serves as the blueprint for the final mold and, consequently, the soap bars. Getting this step right is crucial for achieving high-quality soap products.

I/We promote transparency. This post or site may contain affiliate links. This means only if you make a purchase through these links, not just by clicking, I/we may earn a small commission at no extra cost to you.
As an Amazon Associate, I earn from qualifying purchases
Choosing The Medium
Models for soap molds can be made from various materials like clay, wax, plaster or even existing soap bars. The choice depends on personal preference and the desired level of detail. Clay and wax allow more fine-tuning, while recycled soap bars offer easy handling but don’t mix well with other mediums if you need to make changes to the model.
You should start by gathering essential tools – sculpting tools for details, a sturdy base to work on, and a ruler for precise measurements. Keep your workspace clean and organized to avoid contaminating your model with any unintended waste. For clay and wax models, ensure your tools are sharp and clean for precise cuts and carving shapes.
How to make professional soap-making molds Begins With Shaping Your Model.
Crafting a detailed model involves patience and a steady hand and a little artistry. Begin with a rough shape and gradually carve in the details. Use a ruler to ensure each part of the design is proportionate. Small, consistent movements will help avoid errors. It’s often beneficial to sketch your design beforehand to serve as a reference.
Common mistakes include rushing the process, using unsuitable materials, and ignoring proportions. Rushing can lead to imprecise models, which translates to poor-quality molds. Inappropriate materials might not capture fine details, affecting the final product. Proportions are key to ensuring your soap bars look professional and uniform.
Precision in model making is more than aesthetics. It influences the functionality of the final soap bars, such as ensuring they fit well in their packaging and that they are even comfortable to use. Well-made models lead to molds that produce soap bars with a professional finish.
And don’t forget the last option in today’s tech-savvy world, by far the most expensive option but it is only right to mention it. 3D printing. It would certainly provide a very accurate model but at a price.
How To Make Professional Soap-Making Molds With Rubber. Choosing The Right Rubber
Liquid rubbers come in various types, each having its own unique properties. Liquid silicone is one of the most popular choices, particularly for soap molds. This is due to its flexibility, durability, and ability to capture fine details. However, other options like polyurethane rubber and latex also have their benefits, including price, depending on the specific needs of your project.
Liquid silicone is highly favored for soap molds. Its flexibility makes it easy to demold intricate designs without damaging the soap. Additionally, its durability ensures that molds can be used repeatedly without degrading. And they don’t need any work between pours. These qualities make it a reliable choice for both hobbyists and professional soap makers.
Which Rubber
When comparing liquid silicone with other liquid rubbers such as polyurethane or latex, several factors come into play. Polyurethane rubber, for instance, is known for its excellent tear resistance and versatility, but it can be more challenging to work with due to its shorter working time and harsher chemicals. Latex, being a natural rubber, is more affordable and great for simple molds but lacks the detail-capturing ability and durability for continued use like that of silicone or polyurethane.
Several factors should be considered when selecting liquid rubbers for soap molds. Consider the level of detail required to be captured for your soap bars, the mold’s intended use, and your own comfort level working with the material. If your design is intricate, a soft silicone might be the best option. For simpler designs, latex could suffice. Consider also the longevity of the molds. If you plan to reuse them often, investing in a more durable material like silicone will save time and money in the long run. It will last longer and doesn’t need a release agent and very little maintenance,
Safety
Safety is paramount when working with liquid rubbers. Always work in a well-ventilated area and wear protective gear, such as gloves and a mask, to avoid skin contact and inhalation of fumes. Follow the manufacturer’s instructions closely to avoid mishaps. Proper storage of materials is equally important to maintain their usability and ensure your work area remains safe.
How to make professional soap-making molds with rubber to Usable Soap Molds
Preparing the liquid rubber properly we have already covered “in the use of silicone in crafting” so this link will now take you there for a refresher, should you need it.
There is one point that may be more relevant with soap molds is from which point on the mold will you first pour your rubber then later pour your liquid soal mixture? You may need to suspend your soap model in its tallest elevation to allow the rubber to encapsulate the whole model, and then carefully cut your mold open after its set. this would also be the same method used for demolding your final bar of soap.
A 2 part rubber mold might be your second option, with its locating lugs in between the 2 layers, and then creating a small hole in the least conspicuous place for a small funnel.
Or a plain open-backed mold which will be also your finished product when the soap is made.
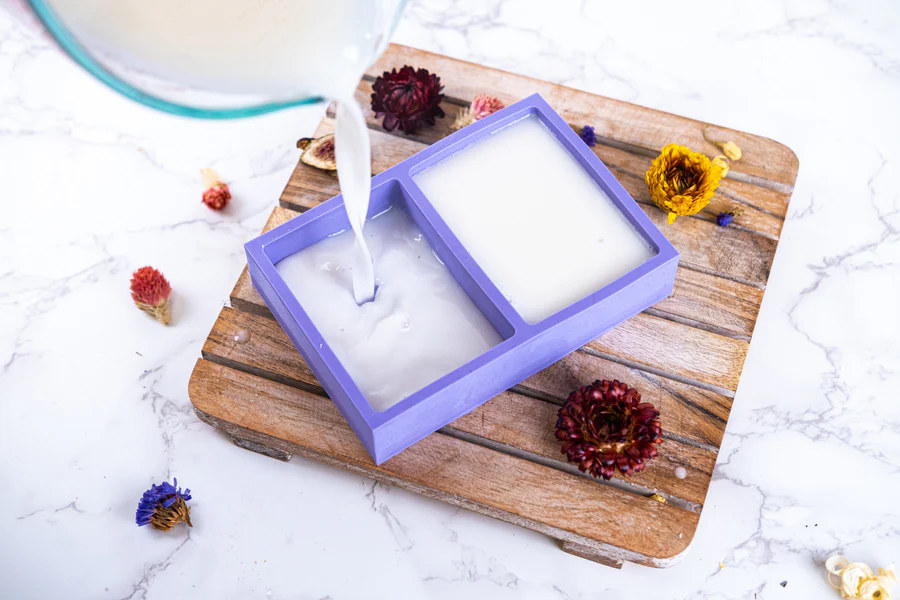
Common Challenges With Soap Making Molds.
Troubleshooting common issues like incomplete curing, air bubbles, or uneven texture is part of the learning process. If the mold hasn’t cured properly, check for errors in mixing or environmental factors like temperature. Persistent air bubbles might indicate a need for adjustments in pouring techniques or the use of a vacuum chamber.
With practice, producing perfect molds becomes easier. Attention to detail at each stage ensures high-quality soap molds, leading to beautiful and professional soap bars.
Contact Us
We hope you find the information useful, but if you have any questions or need help, send us a message. You do have to sign in and confirm these days to comply with government rules. Sorry for the inconvenience.
Author Rob
This article is very informative, especially for those of us interested in soap making. I’m curious about the durability of liquid rubber molds compared to traditional molds—do they last longer, and are they easier to clean? Also, do you have any recommendations for the best types of liquid rubber to use for intricate soap designs? I’m considering trying this method, and any additional tips would be greatly appreciated!
Hi Aris,
If You Go through the article again you will see that each of your questions are answered at least in part. Which rubber to buy is in my opinion silicone in one of its grades, the more intricate your model the softer the silicone the better. I hope this helps you in your choices.
Rob
Thank you so much for your article which is a very interesting read as I had never thought of making my own soap. I found this article very informative and educational which also got me thinking about all the different types of soap I could create for special gifts.
I am due to get married and something like this would could be a good gift to create for my Bridesmaids etc.
I can now understand that with the right mould I could really make soap easily and get quite creative. This article has definitely given me the ability to want to give it a go.
Thank you so much
Imelda